Optimal sizing of powertrain components
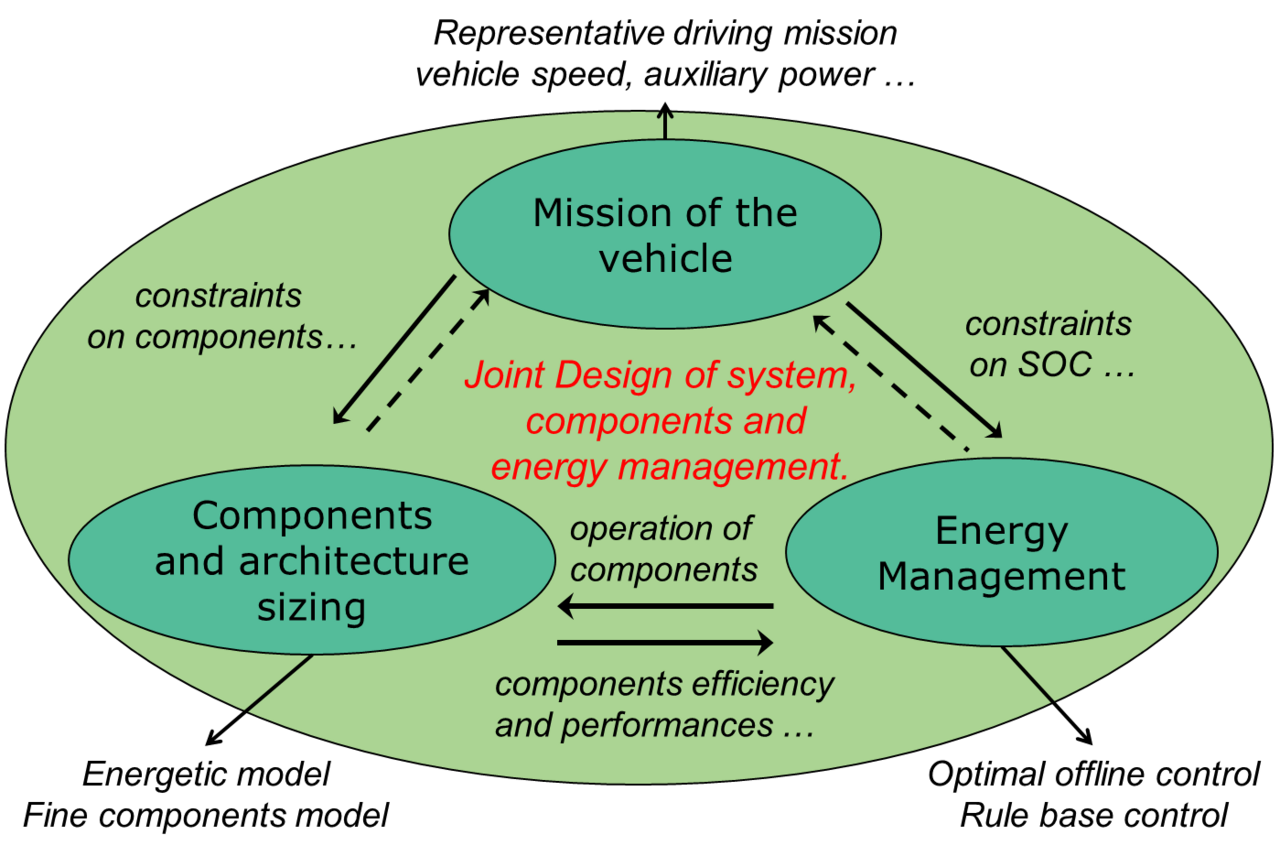
Sizing hybrid vehicles and their components is a complex challenge not easily solved by a conventional sequential approach. Indeed, the process of sizing a hybrid vehicle involves strong interactions between the vehicle’s mission, the sizing of its components and their performance (maximum power, efficiency, etc.), and the management of energy on board the vehicle:
- The mission of a vehicle (driving cycle) imposes constraints not just on the vehicle’s components, but also, for example, on the final charge state of its battery. These latter constraints interact significantly with energy management.
- Sizing a vehicle’s components is not easily accomplished without factoring in energy management. For example, the characteristics of a vehicle’s components place limitations on energy management. In return, energy management determines the operation points of the vehicle’s components.
Lastly, the relative size of components (ICE/electric motor) is also, to a certain extent, a degree of freedom.
To overcome this problem, the team has for a number of years been developing overall cycle-based sizing methods for vehicles and their components.
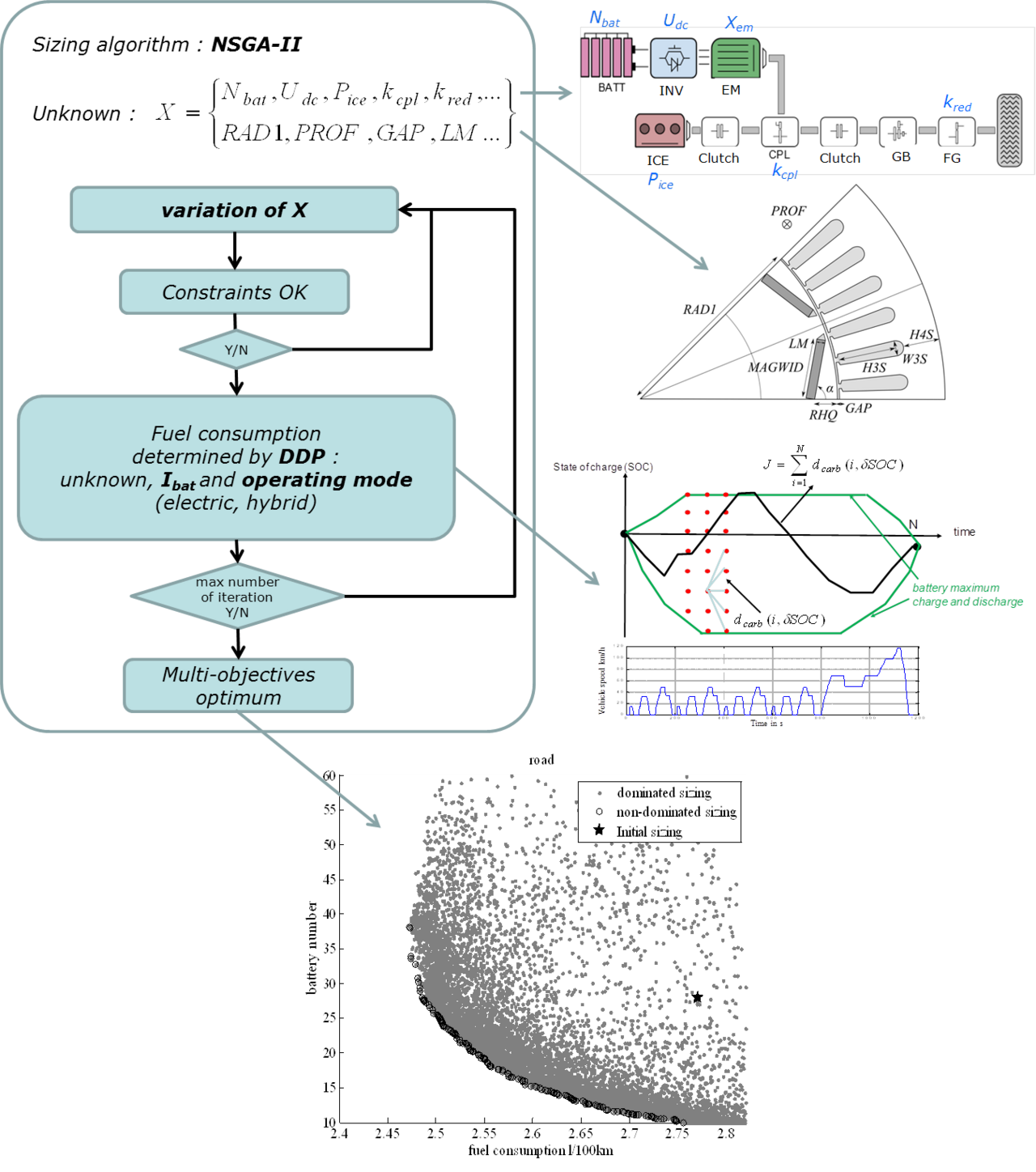
An overall optimisation algorithm is used to manage the sizing of the system and its components in order to scale down consumption, component size, costs, and other aspects. In this case, fuel consumption is itself optimally calculated across an operating cycle. Accordingly, methods for optimal management of on-board energy (dynamic programming) are encapsulated in the overall sizing optimisation process.
The approach has been extended so that the process includes dimensionally accurate models of reluctance components for electric machines. This makes it possible to directly obtain optimal geometries of components on a multi-objective Pareto front. The development of fast, accurate, and geometrically adapted component models is, of course, a prerequisite for studies of this type. Likewise, energy management methods must be fast and robust.
The team is currently working on improving this approach, particularly to take certain phenomena (e.g. thermal phenomena on the machines and system) into account.
Please find more information on the Publications page.